Manufacturing
Manufacturing
Manufacturing facilities are large, complex and re-configured on a regular basis. There’s often machinery and robots from many different manufacturers often with many incompatible SCADA systems. There may also be moving equipment such as automated pallets that can be tracked using a real time location system (RTLS). Adding a digital twin of a manufacturing environment can save overall costs of 20-40% (McKinsey).
Here are three approaches:
Simulation and planning: Whenever a change is made or a new production line installed there will be a ‘debug’ period. Simulating these environments ahead of time can significantly reduce this debug period. Even one hour of production line saved can produce a significant ROI. UrsaLeo’s Gemini platform supports a full range of simulation tools, especially NVIDIA’s IsaacSIM which is used for robots, moving pallets and use physics to accurately simulate the production line. It fully supports ROS / ROS2.0 for the programming of robot operation.
Maintenance/Operations: Our Gemini platform is able to pull data from any SCADA system, from document, asset and maintenance systems and put them in context through the digital twin. This allows maintenance staff to have access to ALL their data in one place in context. Simply click on a piece of equipment to see all the sensor readings, the data sheets, asset metadata and maintenance records. We also provide a Chatbot interface to allow generative AI to be used to access this data. Typically you can find a savings of 20% on maintenance costs.
Training: Manufacturing environments can be hazardous places and using expensive equipment for training purposes removes the equipment from the production line, costing money. Using the digital twin as the basis for a learning management system (LMS) means training can be done safely and remotely, generating further cost savings.
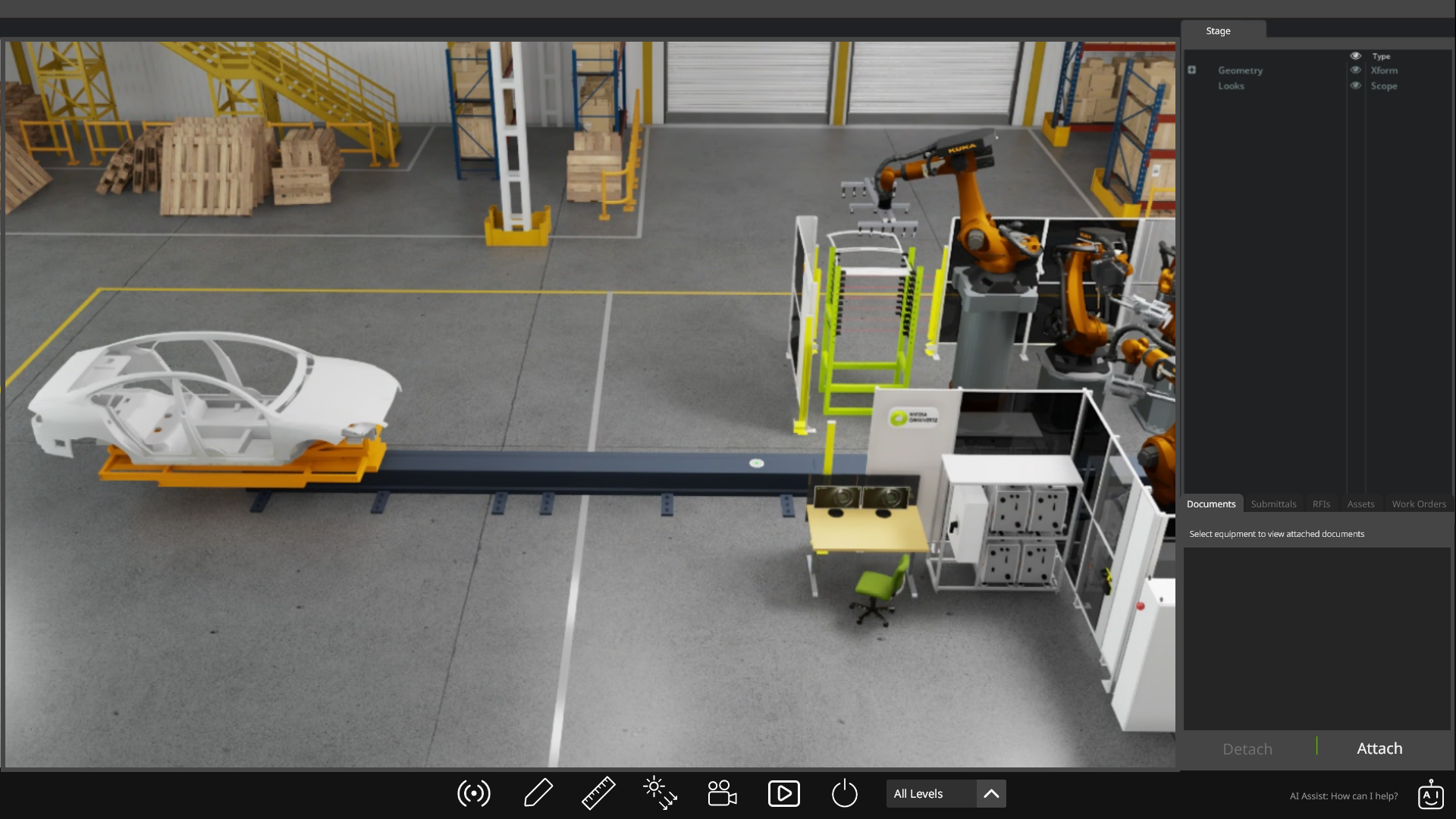